SURFACING TIMELINE
Stages of the lens and the tools used
At MH Optical Labs, we have top notch surfacing equipment that provides accuracy and quality in our products, providing automation and quality control.
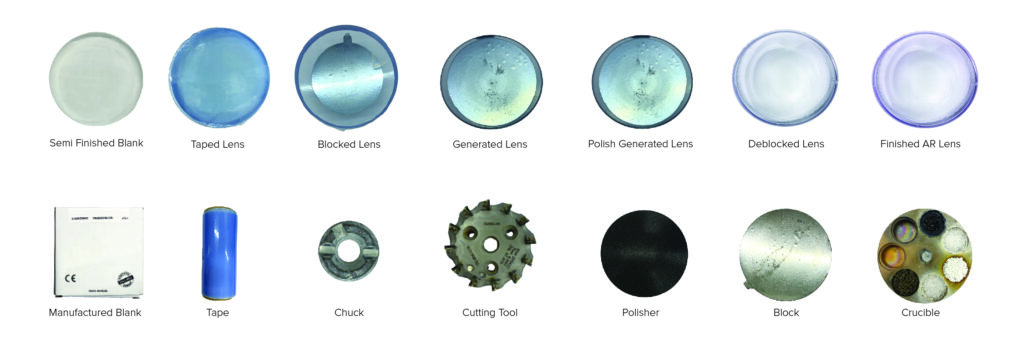
The process of surfacing in our labs begins with the important step of choosing a base curve for a semi-finished blank based on the prescription of the lens to ensure the best outcome for the wearer. Tape is then applied as a protective layer to the already finished front side of the blank to prevent any damage. Not only does the tape help protect the lens, it also helps with adherence to a chuck. The chuck, or block, is what is used to allow the other machines to handle the lens. The blocker machine then aligns the axis, and if needed the prism and decentration is blocked on the chuck. This sets the lens up to accurately be generated.
The generating process is made up of milling, which cuts the bulk of the lens and makes the general curves of the prescription, and turning, which uses a diamond blade to fine tune curves to the nearest 100th mm. Free-form polishing uses a special tool on the generated lens that mimics the back curve of the lens. A polish slurry is applied and the lens is polished until it is translucent. The material of the lens would then determine the next step of the process. The lens could either have a spin hard coating or move on to the AR Lab. Once the lens is ready to move on to the AR lab, the chuck must be removed, or deblocked, from the lens. If it doesn’t already have a hard coating at this point, it will get a thermal dipped hard coating. Finally it moves on to a vacuum box coater where a thin film stack is applied onto the lens to create a finished AR lens. This step concludes the surfacing process, after which the lens moves on to be inspected for quality and accuracy.
This content is restricted to site members. If you are an existing user, please log in. New users may register below.