In The Lab: Look at our AR Coating Facility
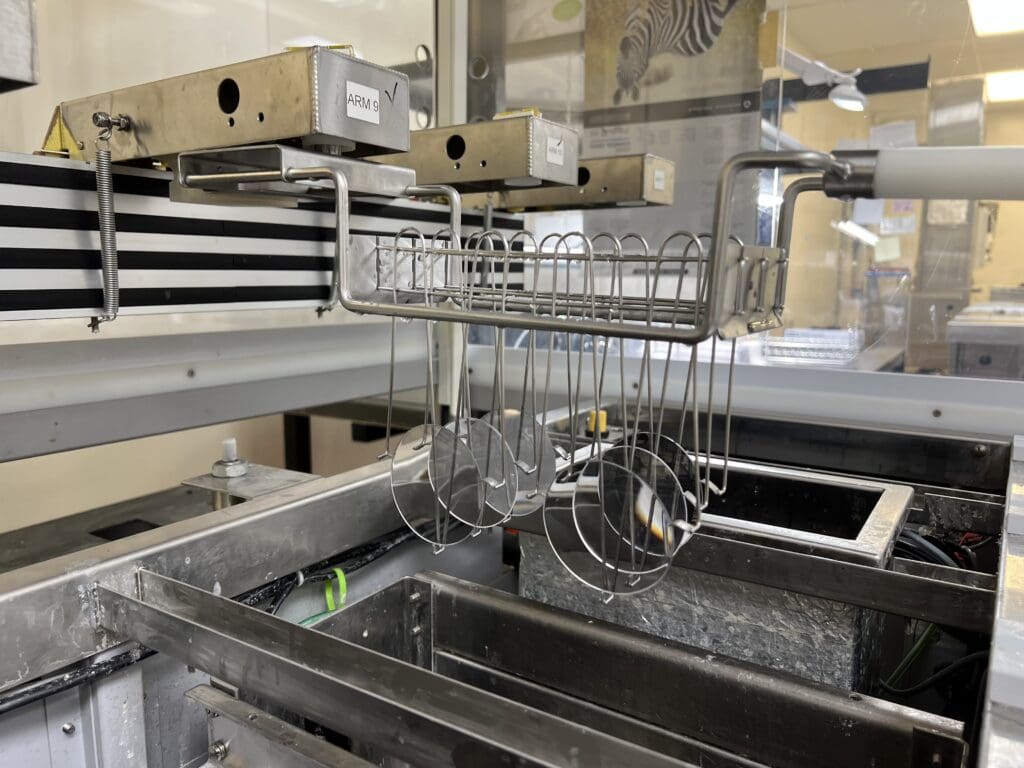
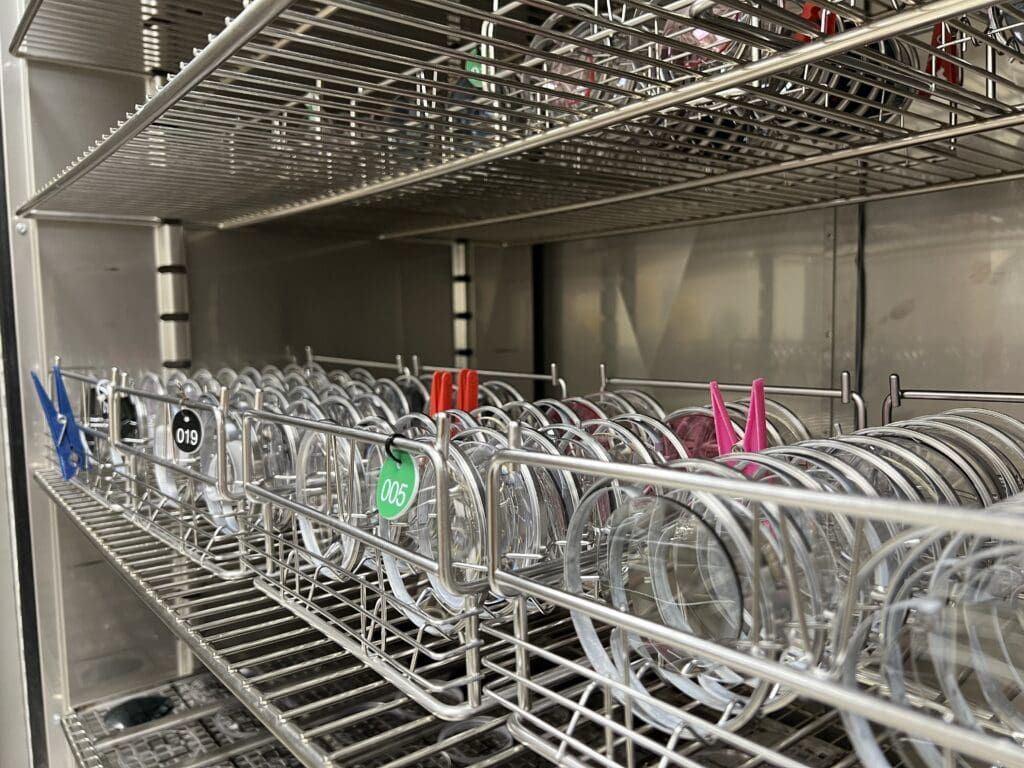
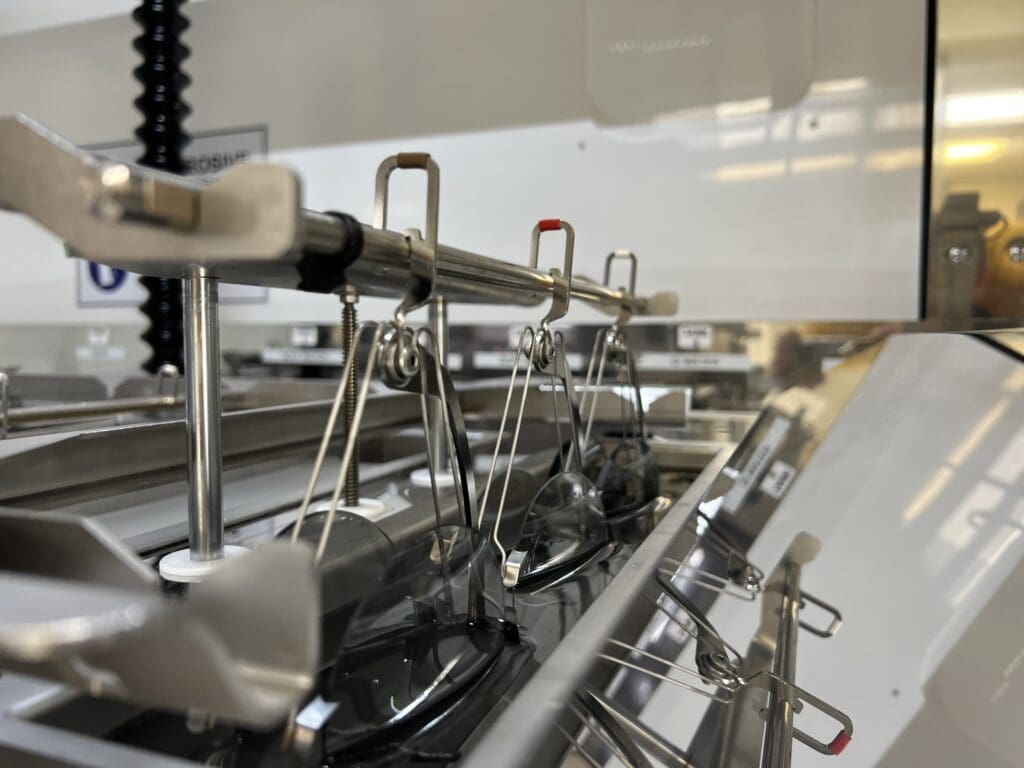
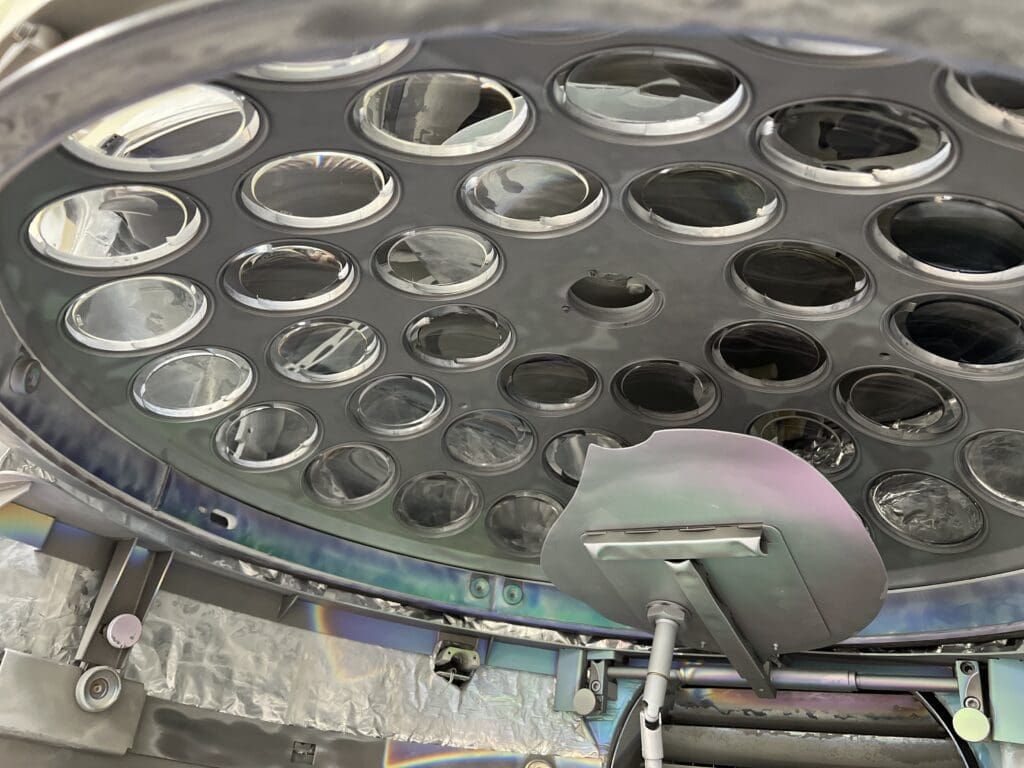
We would like to give our customers a little inside look and understanding of the in house Anti-Reflective (AR) coatings we provide. We offer our own coatings: ARP, SET, Carat Advantage and Granite. We also offer the entire Crizal line in our facility.
Unlike our surfacing department, automation and robotic machines are not a big part of our Anti- Reflective process. It is a very hands on and delicate process that requires very careful handling and attention. In fact, as little as a speck of dust could cause a lens breakage. Our lab operates in a very clean room that is maintained daily to help prevent any outside contaminates.
What is an AR coating? This process applies a thin film stack that adds reflection that will cancel out incoming light waves to allow more light to pass through. This coating lets us see through a lens clearly versus looking AT the lens.
What is the blue/green hue? The color of the AR applied is simply where the wave length falls in the visible spectrum. The color is controlled by adding or subtracting thicknesses in certain layers that are applied.
What is the difference between our house coatings? ARP and SET are the same process; however, we adjust the layers so the colors are different. It is essentially the exact same recipe, but we give the ARP a green color and the SET a blue color. It is all cosmetic preference which color you would like.
Granite and Carat Advantage are a step up in quality because we dip the lenses in a thermal cured hard coat. This makes all the difference when it comes to scratch protection. ARP and SET gets a spin back coat and has a factory front hard coat that is still intact. The dip coat that we apply on Carat Advantage and Granite is far superior after the dip coating is placed into the vacuum chambers and ran as the same recipe as ARP and SET.
Crizal coatings are very similar to our Granite and Carat Advantage coatings. Every lens goes through our strip and dip process that strips the factory front coat off and applies a 1.60 index hard coating. This allows the recipe in the vacuum chambers to be index matched to every lens (1.60) eliminating most aberrations and newton rings that you might see on other AR coatings.
It is important that the process of AR coating is not rushed. The minimum time a job will spend in AR is 3 hours. This is an intricate process that if mishandled and damaged, the job could need to be started over only further delaying the ship date.
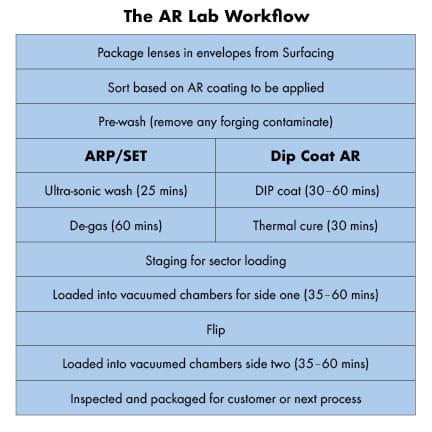
We always recommend AR coating because it not only helps the quality of the lens, improves vision, and reduces eye strain, it also makes your glasses look better!
This content is restricted to site members. If you are an existing user, please log in. New users may register below.